Prof. David Pierce has been elected as a Fellow of the American Society of Mechanical Engineers (ASME), one of the highest honors awarded by the organization. This prestigious recognition celebrates Dr. Pierce’s significant contributions to the field of mechanical engineering, acknowledging years of dedicated research, innovative teaching, and impactful advancements within the discipline. As a Fellow, Prof. Pierce joins an elite group of professionals who have demonstrated exceptional achievements and leadership in mechanical engineering, further enhancing the visibility and impact of their work on a global scale.
Month: October 2024
New Master’s For Digital Design and Manufacturing Innovators
by Claire Tremont
Students can earn this degree remotely from anywhere in the world, offering an accessible path to advanced engineering education
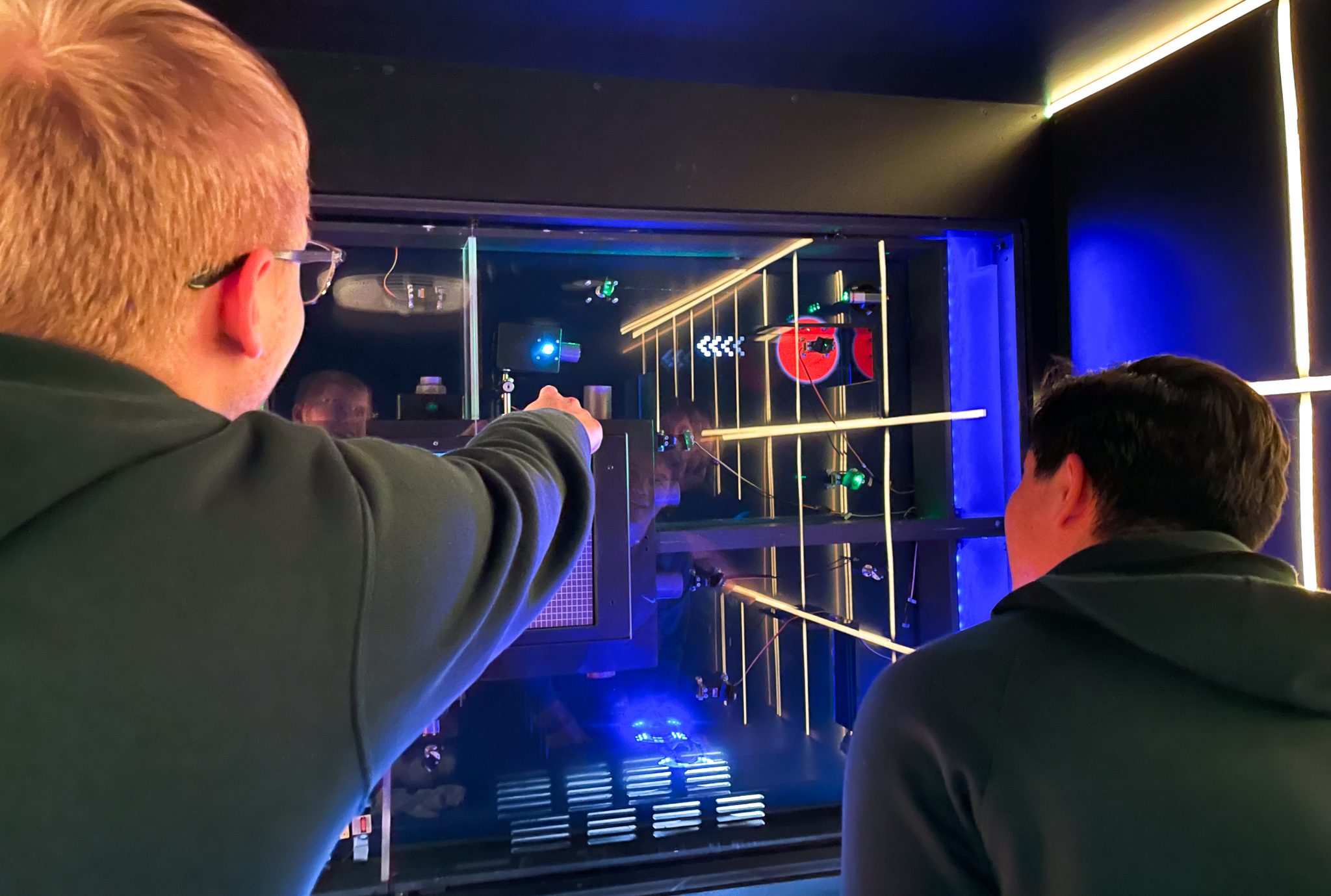
As academia works overtime to meet the needs of a rapidly expanding and evolving industry, one UConn Engineering graduate program is embracing the challenge to educate engineers to innovate with the latest digital design and manufacturing technologies.
The Master of Engineering (MENG) in Digital Design and Manufacturing is a 30-credit online graduate degree for engineers wishing to advance their knowledge in digital tools and models used in modern industries.
Students will learn and master the tools shaping the future of engineering, from digital twins and 3D design software to machine learning and data science, in a part-time program designed for their success.
Together with faculty from the School of Mechanical, Aerospace and Manufacturing Engineering, students will benefit from world-class research and teaching capabilities backed by significant funding from the likes of the National Science Foundation and various Departments of Defense, Energy, and Education funding agencies.
11.1.24 Dr. Pinar Acar – Virginia Tech
Data-Driven Multi-Scale Design of Engineering Materials under Uncertainty
Date: November 1, 2024; Time: 2:30 PM Location: PWEB 175
Abstract: The area of data-driven materials design has been garnering considerable interest due to the increasing need for high-performance materials in electronics, energy and structural applications, and extreme environments. The research on engineering materials and their manufacturing will potentially extend in the future to the development of new-generation composites, alloys, ceramics, and other materials for extreme environments such as hypersonics applications, fabrication of adaptive thermal response materials, energetic composites in fuel cells, thermal energy harvesting in satellites, and materials for green energy applications with the use of computational and data-driven design strategies.
In this talk, Dr. Acar will present an overview of the multi-scale computational methods developed by her research group to design metallic microstructures and mechanical metamaterials for enhanced mechanical performance. The talk will also discuss the impact of manufacturing-related uncertainty arising from the imperfections and defects during processing on the reliability and performance of these engineering materials. Additional topics will cover the integration of Artificial Intelligence (AI)/Machine Learning (ML) techniques into physics-informed material models to accelerate the design of material systems processed with conventional and additive manufacturing techniques.
Biographical Sketch: Dr. Pinar Acar is an Associate Professor at the Mechanical Engineering Department of Virginia Tech. Her research interests focus on multi-scale materials modeling, materials design, design optimization, uncertainty quantification, and machine learning. She received her Ph.D. degree in 2017 from the Aerospace Engineering Department of the University of Michigan. During her Ph.D., she developed various computational methods for studying the multi-scale modeling and design of metals under uncertainty.
Dr. Acar is the winner of the National Science Foundation (NSF) Career Award, the Air Force Office of Scientific Research (AFOSR) Young Investigator Program (YIP) Award, the Dean’s Awards of Excellence: Faculty Fellow and Outstanding New Assistant Professor Awards at Virginia Tech, Frontiers of Materials Award by The Minerals, Metals and Materials Society (TMS), and the International Amelia Earhart Fellowship, as well as the recipient of the best paper award in Non-Deterministic Approaches field in AIAA SciTech Forum 2022. She is an elected member of technical committees in various professional societies, including the American Society of Mechanical Engineers (ASME), The Minerals, Metals & Materials Society (TMS), The U.S. Association for Computational Mechanics (USACM), and The American Institute of Aeronautics and Astronautics (AIAA).
Prof. Norato Elected Fellow of the ASME
Prof. Julián Norato has been honored as a Fellow of the American Society of Mechanical Engineers (ASME). The Fellow grade of membership recognizes exceptional engineering achievements and contributions to the engineering profession and to ASME. The recognition was announced at the ASME International Design Engineering Technical Conferences held in Washington D.C. in August, 2024.
Prof. Nguyen receives multiple large grants from the NIH and the Gates Foundation
by Matt Engelhardt
Through millions in coveted grants, the National Institutes of Health (NIH) and the Bill and Melinda Gates Foundation are recognizing how impactful Thanh Nguyen’s research is to the field of biomedical engineering.
Nguyen, an associate professor of mechanical engineering and biomedical engineering, has already established himself as one of the top-funded researchers at UConn. The NIH is adding to that success by awarding Nguyen four R01 grants totaling more than $9.5 million, with $7.5 million going to UConn researchers.
10.25.24 Dr. E. Farrell Helbling – Cornell University
Taking off: Autonomy for insect-scale robots
Date: October 25, 2024; Time: 2:30 PM Location: PWEB 175
Abstract: Countless science fiction works have set our expectations for small, mobile, autonomous robots for use in a broad range of applications. The ability to move through highly dynamic and complex environments can expand capabilities in search and rescue operations and safety inspection tasks. These robots can also form a diverse collective to provide more flexibility than a multifunctional robot. Advances in multi-scale manufacturing and the proliferation of small electronic devices have paved the way to realizing this vision with centimeter-scale robots. However, there remain significant challenges in making these highly-articulated mechanical devices fully autonomous due to the severe mass and power constraints. My research takes a holistic approach to navigating the inherent tradeoffs in each component in terms of their size, mass, power, and computation requirements. In this talk I will present strategies for creating an autonomous vehicle, the RoboBee – an insect-scale flapping-wing robot with unprecedented mass, power, and computation constraints. I will present my work on the analysis of control and power requirements for this vehicle, as well as results on the integration of onboard sensors. I also will discuss recent results that culminate nearly two decades of effort to create a power autonomous insect-scale vehicle. Lastly, I will outline how this design strategy can be readily applied to other micro and bioinspired autonomous robots.
Biographical Sketch: Farrell Helbling is an assistant professor in Electrical and Computer Engineering at Cornell University, where she focuses on the systems-level design of insect-scale vehicles. Her graduate and post-doctoral work at the Harvard Microrobotics Lab focused on the Harvard RoboBee, an insect-scale flapping-wing robot, and HAMR, a bio-inspired crawling robot. Her research looks at the integration of the control system, sensors, and power electronics within the strict weight and power constraints of these vehicles. Her work on the first autonomous flight of a centimeter-scale vehicle was recently featured on the cover of Nature. She is a 2018 Rising Star in EECS, the recipient of a NSF Graduate Research Fellowship, and co-author on the IROS 2015 Best Student Paper for an insect-scale, hybrid aerial-aquatic vehicle. Her work on the RoboBee project can be seen at the Boston Museum of Science, World Economic Forum, London Science Museum, and the Smithsonian, as well as in the popular press (The New York Times, PBS NewsHour, Science Friday, and the BBC). She is interested in the codesign of mechanical and electrical systems for mass-, power-, and computation-constrained robots.
11.22.24 Dr. Hongseok Choi – Clemson University
Nanotechnology-enabled Manufacturing Processes
Date: November 22, 2024; Time: 2:30 PM Location: PWEB 175
Abstract: The advances in technology and intelligent components, driving innovation in engineering systems or processes, enable expectations to meet the growing demand for enhanced performance and a deeper understanding of mechanisms in a range of applications. While research activities in nanotechnology have exploded over the past decades, the infusion of nanotechnology into practical engineering systems or processes, especially manufacturing processes, has been limited due to the intricate barriers in various manufacturing processes. Appropriate integration of nanodevices into manufacturing processes is crucial for retaining the advanced functionality and performance of the devices in harsh environments. Furthermore, scale-up production of functional materials with uniform incorporation of nanoelements, such as nanoparticles, nanotubes, nanofibers, nanorods, and so on, is essential to leverage the distinctive physical, chemical, and mechanical properties of nanoelements for a wide range of industrial applications. This talk will present two aspects of nanotechnology-enabled manufacturing processes: nanodevice-aided manufacturing and scalable manufacturing of functional materials with nanoelements. In-situ monitoring of several manufacturing processes, particularly friction element welding, an advanced joining process for aluminum alloy to high strength steel, has been successfully achieved with embedded nano-thin-film sensors. The nano-thin-film sensors (embedded or not) would be powerful tools for in-situ sensing at critical locations, thus advancing fundamental understanding of manufacturing processes. In addition, a novel methodology for uniformly incorporating nanoelements into functional materials has been successfully developed for large-scale production of high-performance materials. This nanotechnology-enabled manufacturing process promises to be a transformative technology for further advancing manufacturing processes and economically producing high-performance functional materials for the energy and sustainability challenges facing today’s manufacturing sectors.
Biographical Sketch: Professor Hongseok Choi is an associate professor in the Department of Mechanical Engineering at Clemson University, where he focuses on advanced materials processing, particularly in the realm of manufacturing with a strong emphasis on the interplay between material properties and fabrication methods. He has earned his Ph.D. in Mechanical Engineering from the University of Wisconsin-Madison (UW-Madison) in 2007 and worked as an assistant scientist in Nano-Engineered Materials Processing Center (NEMPC) until 2013, where his work laid the groundwork for various innovations in manufacturing and materials processing. Dr. Choi has authored numerous influential publications in the field, contributing significantly to the understanding and application of advanced manufacturing processes. He actively participates in interdisciplinary collaborations and serves on various committees for professional organizations, fostering growth and advancement within the fields of manufacturing and materials science. He is a recipient of the SME Distinguished Faculty Advisor Award, demonstrating his dedication to fostering the next generation of engineers and reflecting his commitment to education and mentorship. Dr. Choi also engages in active collaboration with industry partners to translate research findings into practical applications, further solidifying the bridge between academia and industry in addressing current engineering challenges.
1.24.25 Dr. Aimy Wissa – Princeton University
Nature in Motion: The power of bioinspired design in unraveling locomotion across mediums and scales
Date: January 24, 2025; Time: 2:30 PM Location: PWEB 175
Abstract: Organisms have evolved various locomotion (self-propulsion) and shape adaptation (morphing) strategies to survive and thrive in diverse and uncertain environments. Unlike engineered systems, which rely heavily on active control, natural systems often exploit distributed flexibility to simplify global actuation and control requirements. This talk will introduce several examples of bioinspired multifunctional structures, such as feather-inspired flow control devices and fish- and insect-inspired robotic model organisms. These devices and systems offer a pathway toward revolutionizing mechanical systems across scales and in different media. The work presented in this talk also highlights how engineering analysis and experiments can help answer critical questions related to elasticity in biological systems, such as the click beetles’ legless jumping. These research topics showcase that biology and engineering form an interdisciplinary two-way street. On one side, natural solutions can inform and inspire mechanical systems’ design. This is referred to as bioinspiration or bioinspired design. The other side is referred to as engineering-enabled biology. On this side, controlled engineering experimental, numerical, and analytical tools are used and developed to answer key biological questions that would be difficult or even impossible to answer directly using the natural system.
Biographical Sketch: Prof. Aimy Wissa joined the Mechanical and Aerospace Engineering Department at Princeton University as an Assistant Professor in January 2022. She is the director of the Bio-inspired Adaptive Morphology (BAM) Lab. Wissa was a post-doctoral fellow at Stanford University, and she earned her doctoral degree in Aerospace Engineering from the University of Maryland in 2014. Wissa’s work focuses on the modeling and experimental evaluation of dynamic and adaptive bioinspired structures and systems, such as avian-inspired and insect-inspired wings and robotic systems with multiple modes of locomotion. Wissa is a McNair Scholar. She has received numerous awards, including the Air Force Office of Scientific Research Young Investigator and NSF’s CAREER awards.
10.18.2024 Dr. Jason Hirschey – National Renewable Energy Laboratory
Thermal Energy Storage for Grid Resilience
Date: October 18, 2024; Time: 2:30 PM Location: PWEB 175
Abstract: The energy sector is undergoing a major transformation. More renewable energy resources are being added to the energy grid to replace aging fossil fuel power plants and meet growing demand. However, these renewable energy resources are more intermittent and rely on favorable weather conditions to produce energy often resulting in a misalignment of energy generation and demand. Thermal energy storage (TES) is a powerful tool to combat this misalignment. This talk will discuss how TES can improve the resilience of the evolving energy grid. Near-ambient temperature TES can complement building technologies to reduce building energy usage for heating and cooling, shift energy usage from on-peak to off-peak times, and extend the capabilities of existing building heating and cooling systems. At elevated temperatures, TES can serve as a peaking resource delivering power to the grid by discharging high grade heat to a thermal power cycle when renewable generation drops or demand rises. As the energy grid continues to evolve, TES provides unique opportunities to further enable widespread renewable energy deployment.
Biographical Sketch: Jason Hirschey is a postdoctoral researcher in the Thermal Energy Systems group at the National Renewable Energy Laboratory in Golden, Colorado. He received his PhD in mechanical engineering from the Georgia Institute of Technology in 2022 on near ambient temperature thermal energy storage for building heating and cooling. His current research focuses on thermal energy and heat transfer with special emphasis on concentrated solar power and high temperature thermal energy storage for power generation.